Home » Outside the box: What our on site assessments look for
Outside the box: What our on site assessments look for
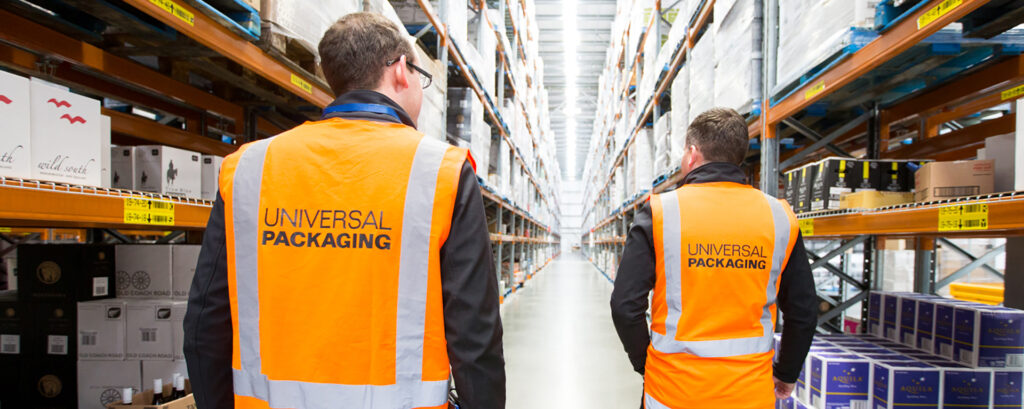
Matt, Garth and Jed each have over a decade’s experience working in pallet packaging processes. But what is it that actually makes them experts? We asked them to take us through what they’re looking for when arriving at a new distribution set-up for the first time.
1. Get a lay of the land.
Jed: “First we’ll scope out a floor plan and ascertain exactly what happens where. At the most simple level, we want to know exactly what type of operation is being run – and there is a massive range here, everything from food production plants to ambient dry goods warehouses to dairy powder plants to chiller/freezer DCs to manufacturing facilities. Each type of operation has its own unique requirements when it comes to how they pick, load, wrap and dispatch their goods.”
2. Check the load.
Garth: “That’s the big question – what are they wrapping? To get the right result we need to ask a whole lot of smaller questions too. Is it an A, B or C profile load? Is it light and crushable or heavy and solid? Are they having any issues with load movement/product damages? How are they moving pallets within their facility and then onto their customer’s facilities? Once we have all this information we can start providing some answers of our own.”
3. Watch the wrap.
Matt: “I’m then looking at all the different variables that go into the wrapping process. Common enquiries here will cover a number of different processes and potential opportunities to increase DC efficiency. How are they wrapping it, by hand or machine, and what improvements can be made? Are they using automated robotic palletisers and inline wrappers? Is output an issue? If so, is the robot or the wrapper the bottleneck? If they are using semi-auto turntable wrappers how are they loading and unloading them? How many labour units are involved?
Could they realise a viable ROI with an automated drive-through system? If they are hand wrapping, have they tried semi or auto wrappers in the past and, if these were too slow, could a robot wrapper be an option? There’s a lot to check!”
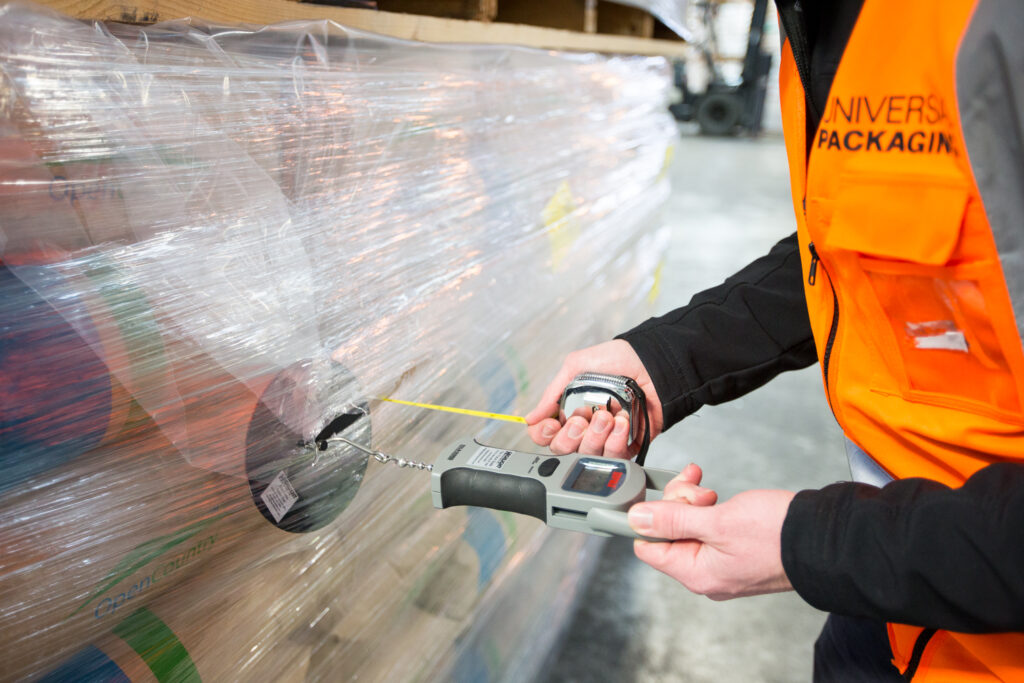
4. Measure the volume.
Garth: “We also rigorously check pallet and pallet wrap volumes. I want to know exactly how much wrap is being used and whether there are any seasonal changes that might impact flow. Ideally, I’ll find out how many rolls of film are purchased each month and how many pallets are dispatched each day, week and month. From there we’ll need to establish how much film is being applied and gain a solid idea of what it’s costing to wrap a pallet. We also need to ascertain if the company thinks in terms of roll price or price per metre –or if they’re looking at their cost per pallet wrapped or actual ‘cost in use’.”
5. Find the pressure points.
Matt: “It’s really important to take your time and carefully examine the entire line, particularly when looking for critical bottlenecks – where these are and why they’re happening. There could be a number of reasons here. They could be staging a lot of pallets prior to and after the wrapping process, for example. In a busy DC, the wrappers might not keep up with the volume of pallets being delivered by the picking crews. In a production plant, the wrapper needs to keep up with the robotic palletiser. Everything and everyone needs to be working in perfect harmony.”
6. Check the user settings.
Jed: “We run a problem-solving process that analyses both the equipment and the people using it. Here we’re checking machine programs are running correct and if the operators have controls at optimum setting. Often we need to check that these optimum settings are even well known.
Then we’re assessing whether the operators are properly trained to check the amount of film applied and the load containment of the pallets they are responsible for wrapping.”
7. Test, test, test.
Matt. “Our approach is ‘if we can’t measure something and show how it will improve the operation we can’t possibly recommend it.’ So we’ll also be checking what the process is for conducting trials at site. We need to know who is involved in the trial process and who are the decision-makers. We’ll also need to know if the company’s current supplier has an arrangement for reporting on load containment, yield and usage, whether they look after the equipment and if they provide breakdown, parts and service assistance. After we have all of this information we can correctly assess all the relevant costs and see where we can cut costs and increase efficiencies and return on investment.”
The seven points above are just part of the testing processes and optimising gains we can deliver to New Zealand’s distribution centres. If you think your operation could benefit from this (and more) efficiency expertise book a site visit in with our team.
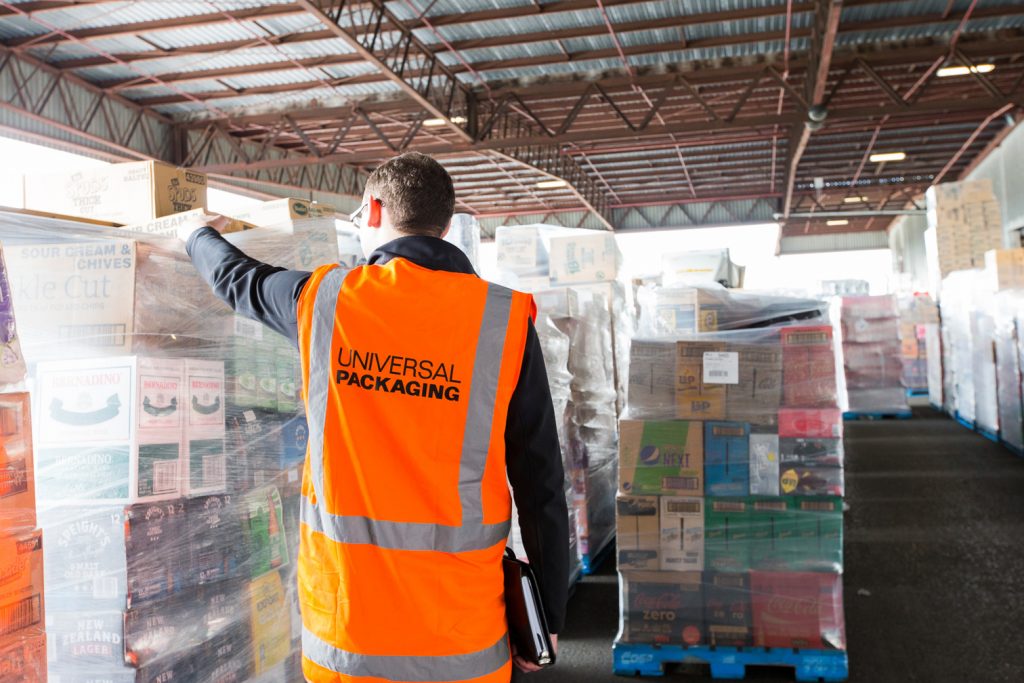