Safety Systems
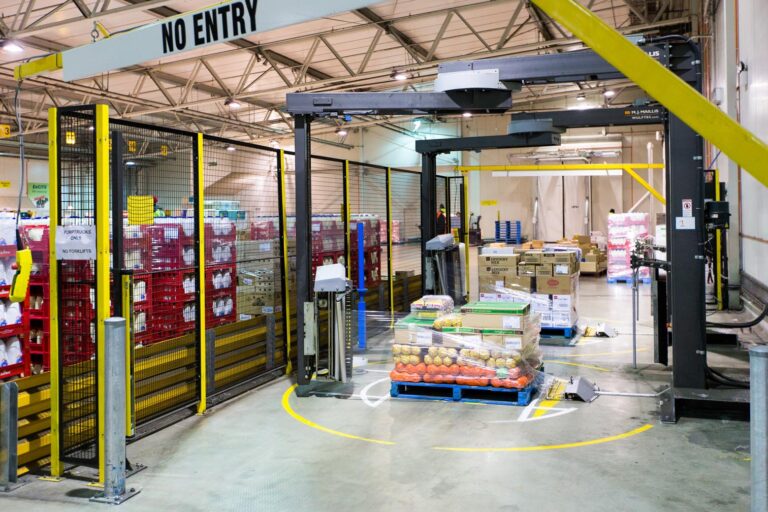
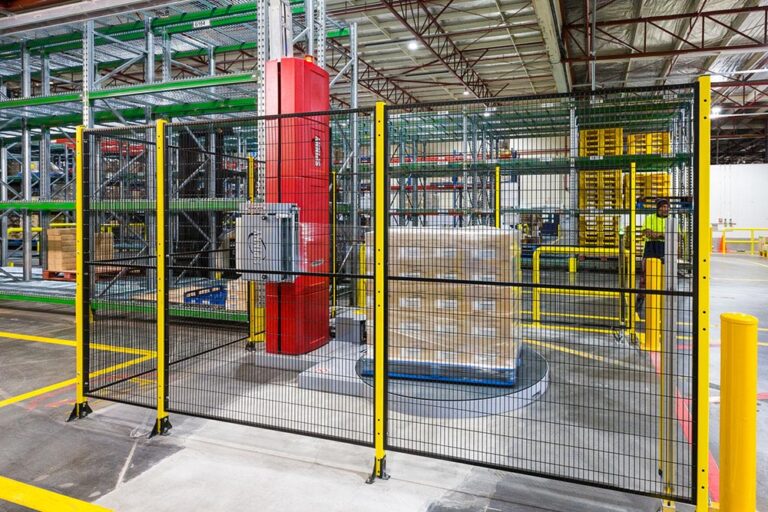
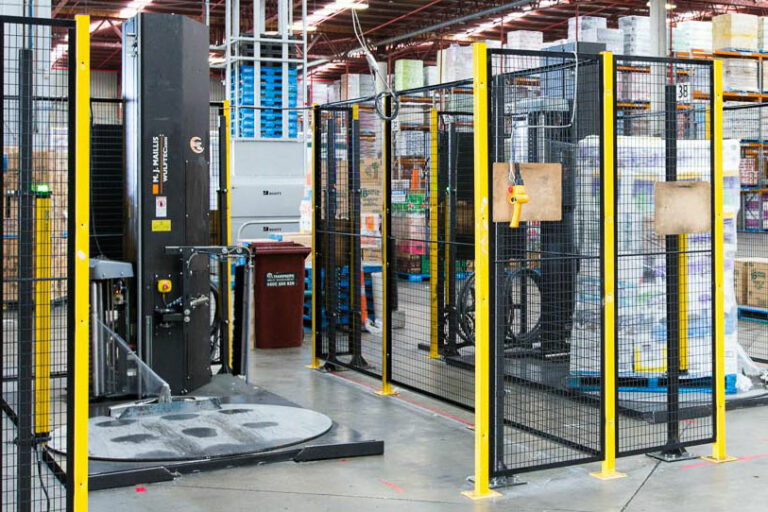
Universal Packaging work with accredited risk management consultants to design systems which integrate with new and existing wrapping machinery. First, we diligently assess all the risks from both equipment and behavioural perspectives. From there we create a system that will actively protect humans while recognising and mitigating the occasionally chaotic nature of human behaviour.
Overall, there are no ‘one-size-fits all’ safety solutions, as no two distribution centres are ever quite the same. So, we always take an ‘individual-Universal’ approach before making specific recommendations on what type of processes and systems to use.
Our team will work with you to establish the most cost-effective method for installing modifications and, most importantly, ensuring everyone leaves at the end of the day in the same condition they arrived.
FAQs
We work with accredited risk management consultants and our clients in scoping and designing safety systems to work with new and existing wrapping equipment, ensuring all measures perform and comply to AS/NZ standards for controls, interlocks and guarding.
One of the most important considerations when planning and installing a pallet wrapping safety system is simple but, also, very complex: everyday human behaviour.
A key approach here is ensuring any system doesn’t in any way hinder productivity. If any additional steps are added to an existing set-up, employees may often attempt to find ‘workarounds’ to keep up with targets. It can wind up with new set-up that’s less safe than before.
So, from the start, we don’t just look at the ‘nuts and bolts’ of any new technology. We help clients develop their unique risk assessment and the features that will then help minimize their risks. Our wider perspective of user behaviour and workplace efficiency and safety ensures a well-designed system is correctly scoped and properly installed.
The balance should always tip towards the human side of the equation – both in protecting them and considering the many idiosyncrasies of human behaviour.
That’s why it is possible to have too many fail-safes or safety processes. If this occurs staff will look for their own solutions to avoid them, increasing the likelihood of accidents. It’s also why we scope sites carefully and always defer to the PCBU (Person in Charge of the Business Unit) when recommending safety solutions. Every system must fit for the process and people it is designed for.
To start with, fencing off equipment reduces the risk of a forklift backing into a machine, causing the need for costly repairs. It also means that only those intending to operate the equipment will be in its vicinity when it is in operation. For the user, there is little change to how the machine operates once inside the barrier, but this extra safety step can help the operator to focus on the job at hand. While safety fencing and light curtains are not yet a requirement by law, many companies are installing them to ensure optimal safety for staff, protection for equipment and ongoing peace of mind.
Some might be surprised by the number of accidents and long-term health effects that occur due to incorrect hand-wrapping technique.
First there is the volume of sound created by the wrap, particularly if the pallet wrap is a traditional blown film product. This can be louder than the average lawnmower when unwrapping, making it difficult to hear any approaching forklift. Long-term hearing damage can occur if the right hearing protection is not work while using this type of pallet wrap.
Then there is the strength and general physicality needed to hand wrap pallets. Walking backwards around a pallet while correctly holding the roll can be difficult. Which is why we always recommend workers bend their knees correctly and wrap pallets using forward-walking application with the right equipment.