Home » Reduced to tears
Reduced to tears
Stretch wrap have you at breaking point? Here are 4 things that may help stop the pallet pain.
Product damage during transportation is obviously one of the main focuses in our work. When pallet wrap tears and breaks occur during transit products move. When they move they can break.
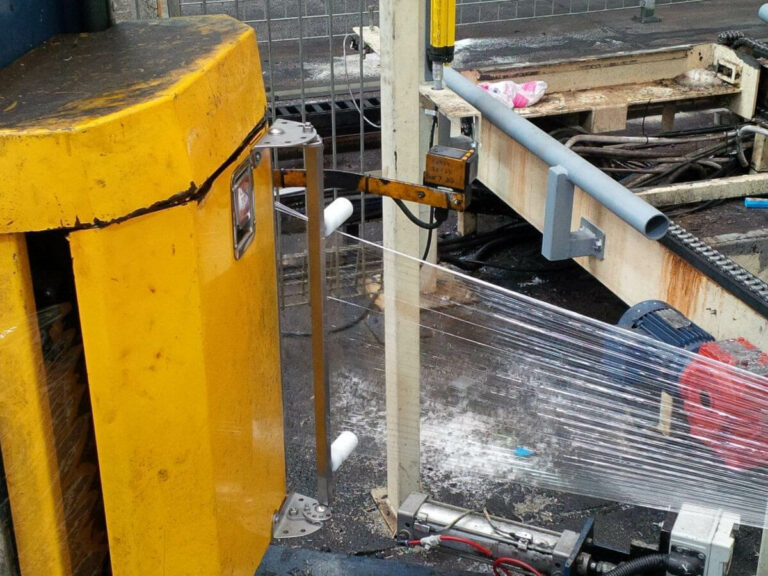
Wrap tearing can cause plenty of headaches before the pallets even make it out onto the road too. Often the solution to the initial tear is simply ‘more wrap’ or to reduce the film tension. But that approach just uses more plastic and doesn’t actually fix the problem – less film tension means more movement within the pallet and potentially more damage later on.
1: Check your load assembly procedures.
It’s not just a matter of checking for product overhang on pallets pre-wrap. Operators also need to correctly assess what elements from within the pallet will move and/or apply pressure on the wrap when everything’s moving. Sharp corners in mixed pallets will always be there – so these need to be contained pre-wrap. Here a few extra seconds during assembly can save a lot more in wrap failure and product damage later on. Correct training is vital – make sure everyone knows what to look for.
2: Keep attention on the tension.
There is no one-tension-fits-all setting on your pallet stretch wrapper. Nor can any hand-wrapping process perfectly bind every single pallet. Instead a careful initial analysis of film tension settings needs to be undertaken to hit the ‘sweet spot’ – where there’s no film breakage, no excess movement of pallet contents and no crushing of the load.
3: Be a roll model.
While some of the new machine and hand-wrapping products are far more durable than past options it still pays to carefully look after each roll of wrap. Damage to film from mishandling or dropping can result in small imperfections in the roll that can then severely compromise the integrity of the wrapping performance. And make sure each roll is correctly installed in the machine too – it’s surprising how often a she’ll-be-right approach here is oh-so-wrong for the pallet.
4: Call on the experts.
The ongoing actual cost of wrap tearing can often be hidden within a range of data. So if there are ongoing tear incidents it pays to get an expert in sooner rather than later. An initial process and equipment audit will help provide far greater clarity here. This assessment will take into consideration both the small details and ‘big picture’ of pallet and product life from picking to packing to transport, delivery and end use.
Preventing wrap tearing is a big part of our everyday work and we always appreciate the chance to get out on site and help out. It may be that some refinements can be made to equipment settings. Or a new film will be recommended to trial. Or a firm word and helpful demonstration with the team is needed.
If you’d like an on-site audit or a trial roll of the latest and greatest stretch wrap available, simply flick us an email. One way or another, we’ll improve the performance and end the pallet pain.