Home » An order to go
An order to go
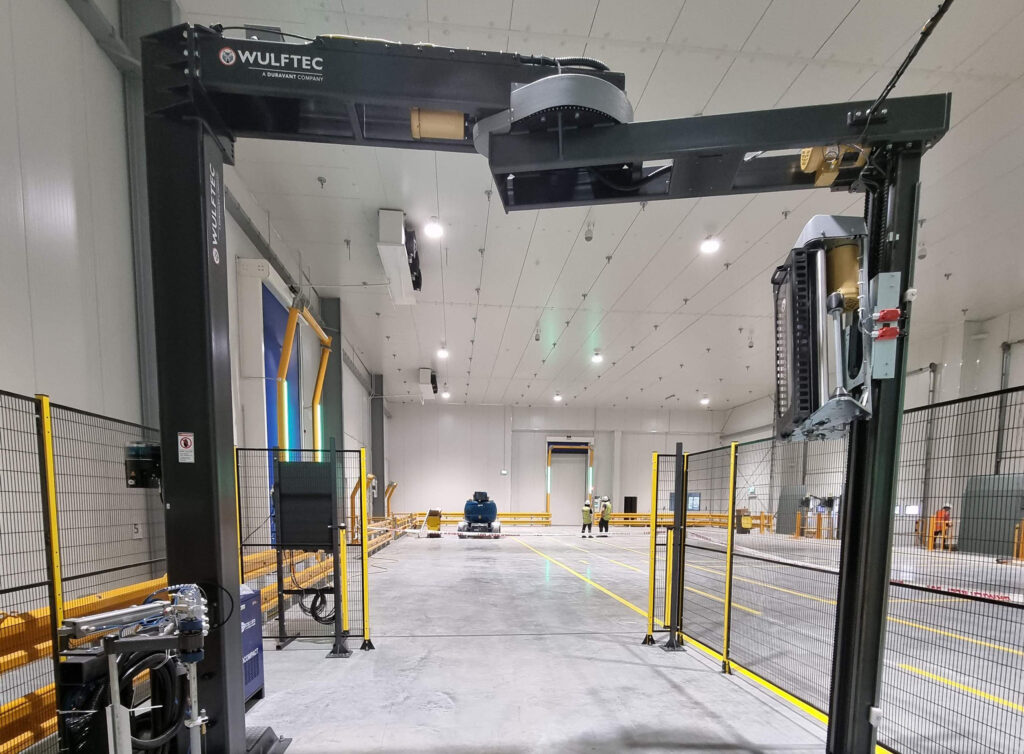
Mark Bavister has been busy of late. As Martin Brower Country Manager for New Zealand, he’s been a key part of a big change for the company as it has moved into a new distribution centre.
Martin Brower are responsible for the provision of 4th party logistics for restaurants throughout New Zealand, wrapping ambient, chilled and frozen packages – everything from eggs to cups, bread to burger boxes.
Everything must be packaged with optimal speed and efficiency, the substantial throughput carefully managed to ensure the highest of standards in food transportation. However the company had been hamstrung by the size and capability of their building.
“The original facility had been built in 1987,” says Mark. “So we were in there for 35 years – and probably outgrew it ten years ago.”
Achieving the right size and scale was an important element of the move. Compared to the 3500sqm of the old facility the new building has 10,000sqm and 10,000 pallet spaces.
As part of the project build Martin Brower also looked at the containment requirements. It’s an important part of the operation to get right, particularly given the different types of packaging needed.
Two WRTA-150 rotary arm wrappers with drive through safety systems have now been installed at Martin Brower.
“We now have one in the ambient area and one in the ELA (Environmental Loading Area) on our dock, which serves the frozen and chilled chambers,” says Mark.
This is a major step up from the single turntable wrapper at the old site, where “we basically could only wrap one pallet at a time.”
One major improvement with the new equipment is the ability to wrap large or unstable loads. As the rotary arms avoid spinning the load, unstable pallets can be securely and safely wrapped. Pallets up to 2.6 metres high can be wrapped.
“Pallets going locally don’t need as much wrap as those with longer travel requirements,” says Mark. “The new machines are programmed with different wrap patterns. Changing those with the push of a button is extremely helpful.”
This operational flexibility of the new equipment is a major drawcard for the busy distribution centre, and Mark is confident the new set-up is ideal for any new approaches to come.
“A traditional turntable wrapper is limited. However the Wulftec equipment can wrap more than just pallets,” Mark says. “We’re wrapping cages, half pallets and carts, and in the future we’ll be wrapping different types of material too.”
“We’ve developed our own type of small pallet that fits through a doorway – it’s half the size of a standard Australian ship pallet. Because of this smaller platform, having the pallet on the ground makes it quicker and far more efficient with the new rotary arm wrappers.”
After two weeks of operation in the new DC “everything is going as planned.”
“It’s very easy for the employee to use and most of the time they simply push one button – so it’s drop, push, wrap, pick up,” he says. ”Being fully automated it saves a lot of time.”
“Having the two (Wulftec wrappers) means we also have the redundancy should we ever have a breakdown,” Mark says.
The focus is on far more than just continuous operation however. Team safety is “the most important thing in our business,” according to Mark.
The new equipment delivers ongoing peace of mind for Martin Brower. There are multiple safety features that help, with the separate packing area, heavy-duty safety guarding, light curtains and wrapping processes combining to protect the busy team.
Along with the Wulftec equipment the new DC also has a Spinny S300, which is responsible for wrapping the buns that come out of the bakery.
“These come on a 1200×1200 pallet that has been made specifically for this product. The Spinny ensures we can palletise the bun crates, wrap them quickly and properly, and then get them straight into the blast freezer,” says Mark.
The Universal team will soon be back on site to create new programmes according to Martin Brower’s needs. The working relationship between the two companies is a strong one, ensuring Mark and his team could move with confidence when the time came to choose the right equipment.
Universal’s Jed Goudie helped with this by taking the Martin Brower team on-site at another DC to see the WRTA-150 in action, an approach Mark says was “a massive help”.
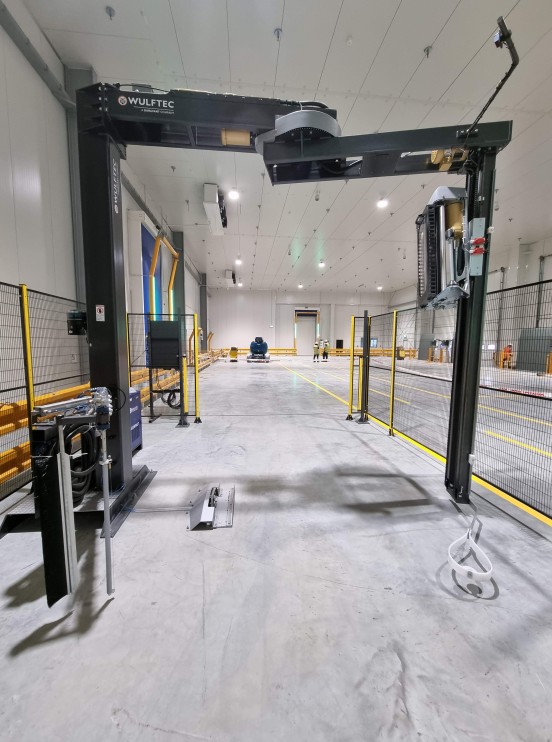