Home » Pack and save and save and save
Pack and save and save and save
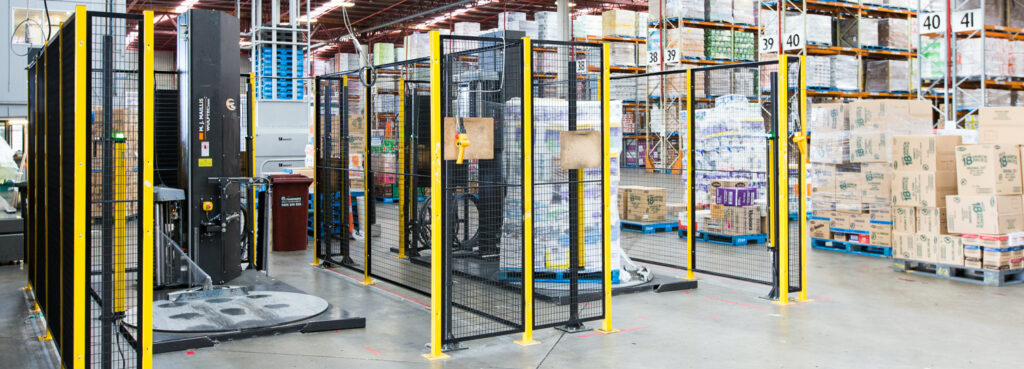
As New Zealand’s biggest grocery distributor, and one of the country’s largest companies, Foodstuffs employs more than 30,000 people nationwide.
Foodstuffs North Island alone supplies 96 New Worlds, two Fresh Collective by New World, 44 PAK’nSAVEs, one PAK’nSAVE Mini and 179 Four Square owner-operated retail supermarkets. Then there are the 81 Liquorlands, one Shoprite and one Write Price retail stores and seven Gilmours wholesalers.
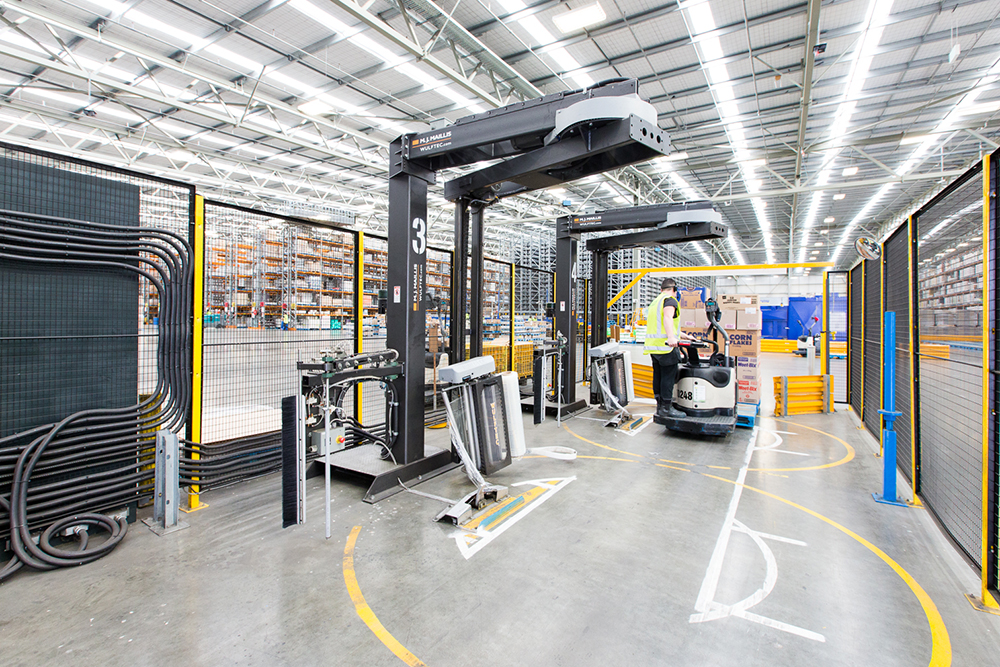
“We used to have people hand-wrapping up to 400 a day, and that resulted in a lot of pain and discomfort for our operational staff,” says van der Steen. “By having the consistent wrap on all our pallets our in-transit damages disappeared altogether,” says van der Steen.
Along with the new WRTA system Foodstuffs are making the change to Nanowrap, ensuring they can save on wrap used while wrapping with consistent strength. Peter van der Steen states that this is simply “faster and cheaper”.
Being able to innovate and improve on a regular basis is a big priority for the company, and a major reason for their success.
Prior to 2010 over 80% of wrapping throughout Foodstuffs distribution centres was done by hand. Any old turntable wrappers being used were not up to the new health and safety standards and were extremely labour intensive, with staff having to operate the machinery full time.
Now, with the increased automation, new safety systems and advanced pallet wrap significant gains have been made with the reduction of labour and an increase in pallet throughput.
Universal have now installed a total of 25 WRTA150 machines in Foodstuffs DC’s across the country.
The previous areas required for pallet staging areas are no longer required, which provides plenty of extra storage space. Material handling equipment is also kept to a minimum with the wrappers being loaded and unloaded by low level order pickers (LLOD). There’s no need for other equipment generally needed for wrapping pallets like counterbalance fork trucks, pit mount wrappers and ramps and touch points are kept to a minimum.
Indeed, the only human contact needed with the WRTA system is when it comes time to change the roll of film.
Wrap use is also heavily reduced thanks to the power pre-stretch carriage. Every little gain here can make a big difference to the bottom line.
“With the scale of Foodstuffs operation we can make small changes that can have large positive effects,” says Universal Packaging’s Equipment Specialist Jed Goudie.
“For example, by increasing the gear ratio on the equipment and running our new Nanowrap film, Foodstuffs will save the equivalent of 18.5 million single-use grocery bags per year.”
The massive scale of Foodstuffs’ operation requires a diligent and expert perspective on every aspect of the supply chain. The Universal Packaging team are proud to help this New Zealand owned and operated company, and look forward to even greater success in the future.
Check out the video of the equipment in action here.