Home » The focal point of packaging
The focal point of packaging
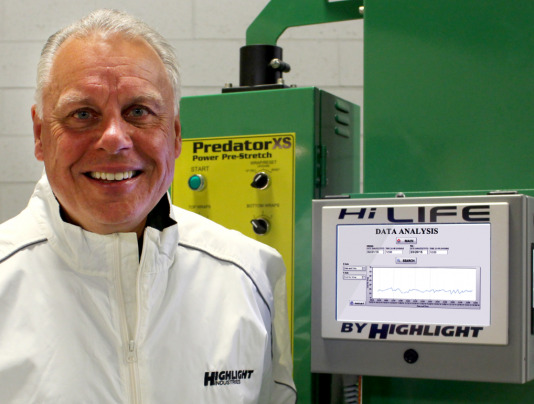
In 2015 Universal Packaging partnered with U.S firm, Highlight Industries. The world-leading pallet film testing equipment from the Ohio-based company provides us with the means to collect, record, and graph data in real time during site visits. Their Portable Film Force System is the most accurate way we can determine ultimate containment force across a palletised load.
The ethos that has driven Highlight forward is one very similar to our own. It’s why we travelled to their head office for training back in 2015, and why we continue to meet and maintain a close relationship with the innovation-focused company.
It’s also why we’re always interested in what Kurt Riemenschneider has to say, the Highlight manager’s decades-long experience always providing plenty of valuable stretch wrap food for thought…
What made you first decide to develop and build stretch wrap equipment? What were you doing in your late 20s, early 30s that sparked that fuse?
In May I marked 40 years in the business. It started properly in the mid 80s when I saw firsthand that equipment couldn’t maximise the film wrap properly. So the work began on an adjustable pre-stretch system. Since then we’ve continued to develop our equipment and grown into an industry leader. We’re working with a wide range of multinationals to ensure their packaging performance is at optimal capacity.
What do you consider are key factors behind Highlight’s success?
In 1997 we built a multimillion-dollar facility in Wyoming. Back then we made sure it was equipped with state-of-the-art equipment and staffed with the very best people we could find. While we’ve innovated our technological capability our hiring approach has stayed much the same.
That’s a massive part of our success – the team here. In our lab we now have twenty-five equipment specialists and four packaging engineers. Everyone is passionate about continuing to push what is possible in our industry.
We also work closely with Michigan State University, who have a reputation as one of the best packaging universities in the world. We’ve been very fortunate to get the right people. They’re looking for a challenge. They’re looking to do different things in different ways.
Why is it so important to test stretch wrap performance?
There are two different ways of looking at stretch film. Often, particularly in the past, it has been grouped as a commodity. Companies buy it in bulk and think the wrap is essentially all the same. So purchasing decisions are made on cost per roll.
However there is a significantly different way of looking at things – and the science of stretch film is considerable. It starts by looking at the ‘sweet spot’ within the forces of containment and how much force is at play within the stretch of the wrap.
We look at stress/strain curve and with clear analysis establish the sweet spot – and then continue to monitor this. A lot of companies don’t keep an eye on their wrap performance. They think they’re stretching by 230% but in reality they’re often not even close to this figure.
What are the key aims of your work?
So, cutting wastage is one focus. But then there are the figures associated with damage. Wrap breaks, pallets collapse, products are broken. .05% of everything shipped in the United States is unsellable. It seems a small figure, but when you consider the quantities involved this is absolutely huge.
These products usually can’t go back to the distributor either. It goes to a dollar store, or is sold to a recycling centre, or simply goes to landfill. With the monetary costs and carbon emissions being so high it is worth wrapping right.
What’s the best part of your work?
The best part is getting a challenge. We just had a bottled water manufacturer come to use with a new product. They were doing a 15 pack compared with a 24 pack in the past. They came to us and said it was a big promotion introduced for end of aisle use in grocery – then we shipped all the loads out and they fell apart. They then came to us with their loads. We set up the lab and got our senior guys here to work every angle.
We showed them the different stacking patterns. We came up with different solutions then we went out in the field and implemented it and monitored it. And that customer saved $4.5 million in the first year by implementing these recommendations.
So we look for challenges. Yes, there’s the everyday work. But the unique challenges and the lab stuff are the fun stuff. And the return on investment and the appreciation we get from customers… The biggest thing we hear from customers is “why didn’t someone tell me about this before?”
Do you think many companies understand the real costs associated with their pallet wrap and how it affects productivity?
Some certainly do. I was on a site visit and saw a sign on a fully automated machine there: ‘For every minute of downtime on this machine it costs $15’.
One film break would take five minutes to fix. So that’s $75 per break – more than the cost of the roll. If they didn’t maintain the equipment they were losing a lot of productivity. And that’s where a good plant manager can make all the difference.
How important is sustainability to Highlight’s work?
Sustainability is a hot topic right now but, despite the increase in awareness, it’s still often misunderstood. It can be easy for companies to still focus on the wrong things for the right reasons.
Here product damage should always be one of the most important considerations. These damaged products are ending up in landfill, making far greater an impact than what is generally perceived.
That’s why it’s vital that the performance of the wrap is a primary focus. For certain applications a bio-film may perform well. However it needs to be carefully measured and the results need to be quantifiable. So we essentially say we can work with every type of wrap. But we’ll set up and test all options to ensure the true lowest impact on the environment.
What do you see in the future of Highlight Industries?
One thing I can say for sure – there will be far more of the ‘we don’t sell stretch film, we sell the solution’ approach. So that’s the film and the equipment working together to give companies the very best results. And it’s provided along with technologies to monitor it, technologies that can see every load being wrapped, as it is wrapped.
Covid has pushed this innovation along, as people can’t go out into the field to undertake film audits as easily as they could in the past. So now monitoring systems have become so much more important.
The ability to connect through 5G will make a connected world so much better, more technical, and more specific in how it deals with problems and delivers results. Sure, companies don’t have to adopt it. But this technology will provide huge advantages.