Home » Return to sender, expense unknown
Return to sender, expense unknown
In 1962 Elvis Presley crooned “Return to Sender” – a song about a forlorn man who kept sending mail to a former sweetheart, only for it to return each day, ‘address unknown’. It’s a sad situation the modern company knows only too well. Only, their goods are returned due to product damage. And the cost can be far more than a little heartbreak.
Speed, cost, and convenience has transformed distribution requirements around the world as new technologies have transformed both how people shop and how companies store and send products.
But what is the cost of this convenience? How do Kiwi companies ensure secure, sustainable shipping without compromising their bottom line? In the battle of bigger-faster-more, can we truly have it all?
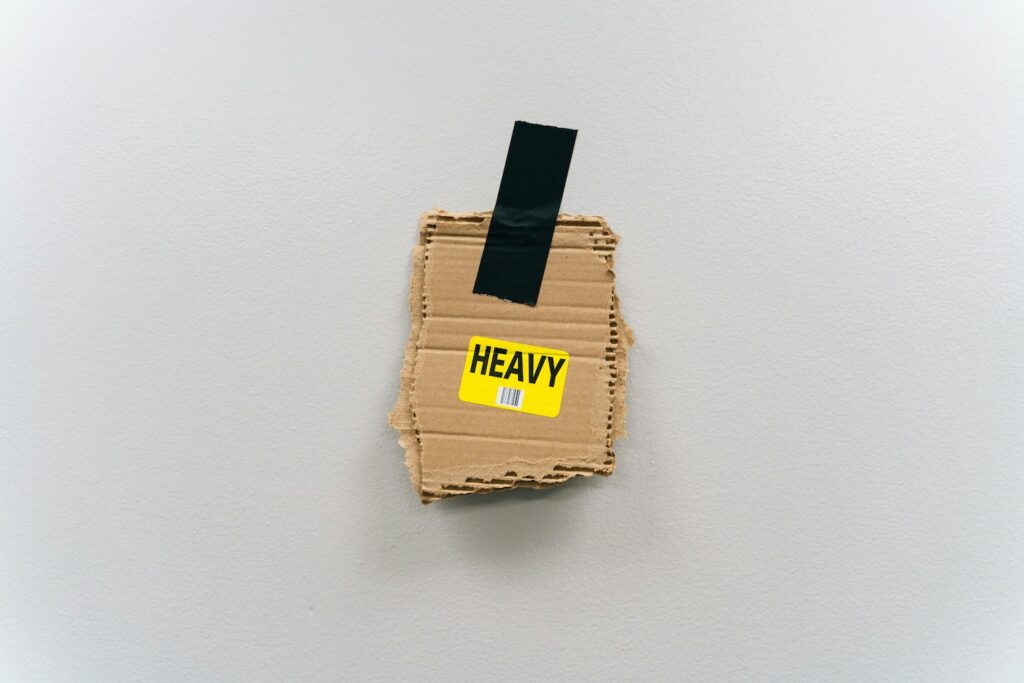
Nobody wants to talk about product damage. It is a muti-faceted problem with no easy answers. Yet it’s an everyday problem. From the product being picked at the factory, to prepared for sending, to packed, stored, dispatched and transported, there is huge potential for damage to occur – and the consequences can be major.
First there is the obvious impact of goods going to landfill, and the replacement value of these goods affecting profit and productivity. One of the main reasons products are destroyed is the cost of repair and the cost of storing unsellable products. For damaged items that cannot be resold, recycled, or repurposed, storage costs will rarely be recouped.
Then there’s the environmental impact from the additional packaging required to re-wrap and re-send pallets. It’s not worth saving initial costs on inferior wrap if two or three times as much stretch film is subsequently being used.
It is also worth considering the negative impact on brand reputation, with the unnecessary waste of some companies often resulting in considerable online attention. In addition, extra goods equal more weight equals additional fuel costs – and the time needed to correct any issues.
Even if a pallet of goods is quickly recognised as being damaged there is often no quick fix or magic answer. Indeed, there’s considerable potential for further inefficiencies to echo throughout the supply chain. As illustrated in the example below, the disposition process can be complicated.
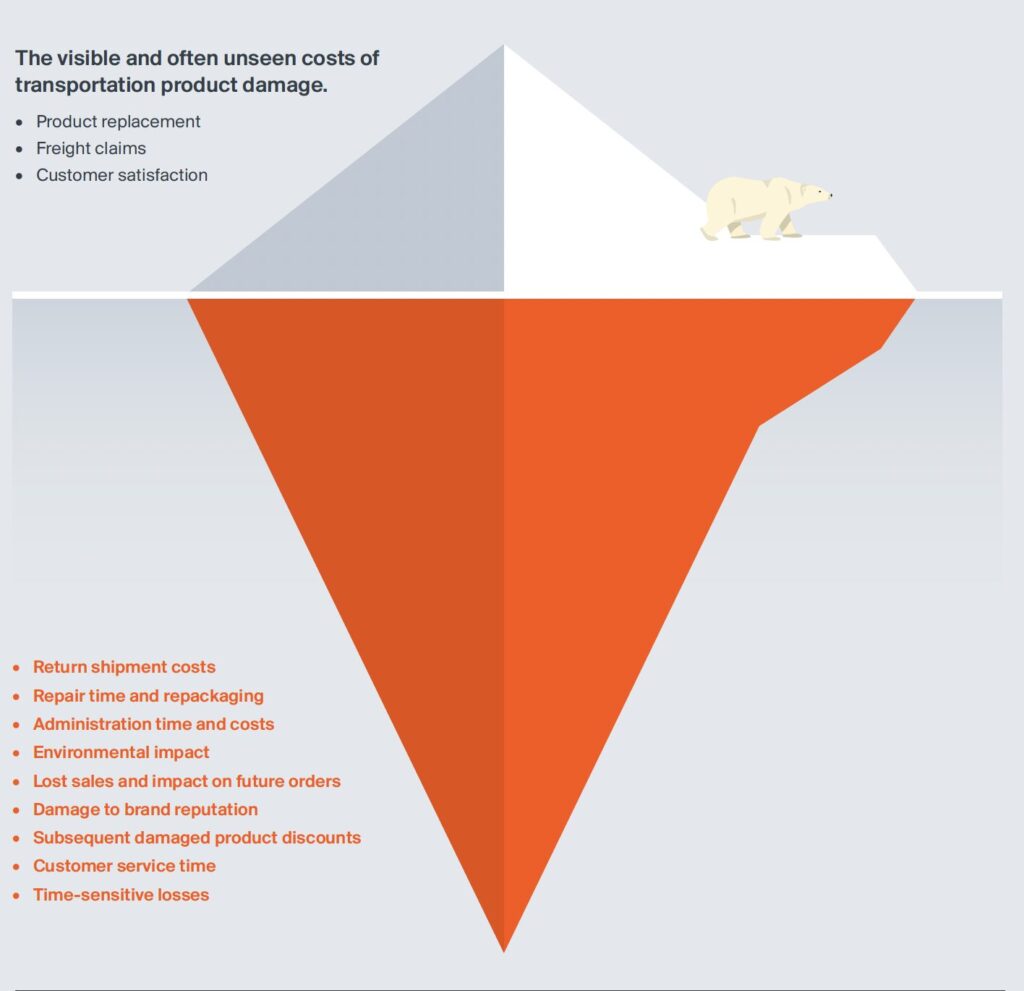
“Nobody wants to talk about product damage. It is a muti-faceted problem with no easy answers.”
One of the most impactful ways brands can decrease their impact on the environment is to reduce incidents of damaged goods. This means looking at the big picture and testing how small changes to individual packaging products and processes can affect this result.
This requires a total cost approach to packaging, bringing all departments together to ensure testing and analysis is correctly undertaken. An Operations Manager will be looking to achieve high speed and efficiency, Procurement may be assessing how to cut costs, and Sustainability Managers will be aiming to reduce waste. These three departments need to work together to find solutions that help everyone.
When it comes to effective pallet containment, this work begins with accurate measurement. At Universal Packaging we appreciate the chance to get on site to ensure the exact right amount of film is being applied with a precise amount of tension to hold the load in place through sudden braking or sharp turns.
This is governed by an international standard, called the Standard Guide for Performance Testing of Applied Stretch Films and Stretch Wrapping ASTM D8314. It’s important business to get right.
A packaging assessment starts with containment testing. These tests involve analysing how much the wrap yields under pressure, which is dependent on the shape, size and density of the load, and carrying out various measuring processes.
The data collected provides valuable clarity into exactly what wrap to use, and how much is needed – and can result in significant stretch film reduction and cost savings.
We also often employ a tilt test. Once loaded and wrapped, the pallet is tilted on various angles to place it under a range of stresses, simulating the movements it may encounter when being transported.
This measures the effectiveness of the current film and wrapping techniques so they can be improved if needed. The pallet must be able to withstand a sideways tilt angle of at least 26° before showing signs of any significant distortion.
“When a delivery exception occurs, there are several options for disposition. Maybe the product will be dropped at a local warehouse to be restacked, reworked, and redelivered. Or it could be donated to a local food bank. It may even be thrown in a nearby landfill. It also could mean that the driver needs to bring the freight back to the origin or another location so the product can be returned or sold to someone else.
In general, the disposition process takes time. Determining product value, potential for rework, locating nearby warehousing solutions, locating a nearby food bank—this can take anywhere from minutes to days depending on the effectiveness of the strategy in place.
All the while, the driver most likely has another load to pick up that day. If he isn’t given disposition immediately, chances are, he will miss his next pickup.”
“What Makes an Effective OS&D Strategy?” C.H.Robinson
“We appreciate the chance to get on site to ensure the exact right amount of film is being applied with a precise amount of tension to hold the load in place through sudden braking or sharp turns…”
Bigger distributors can take advantage of our unique SCOPE system. This technology monitors all pallet packaging use and creates clear reporting. In this way busy D.Cs can accurately test new pallet film before committing to change. SCOPE is also helpful for alerting when too much wrap is being used – if any set parameter is changed it is quickly discovered and fixed.
With this accurate measurement and expert analysis some of the key causes of product damage in transport and storage can be mitigated, saving a huge amount of time, cost, and stress.
If you’d like to book an on-site packaging assessment with one of our containment experts get in touch today.
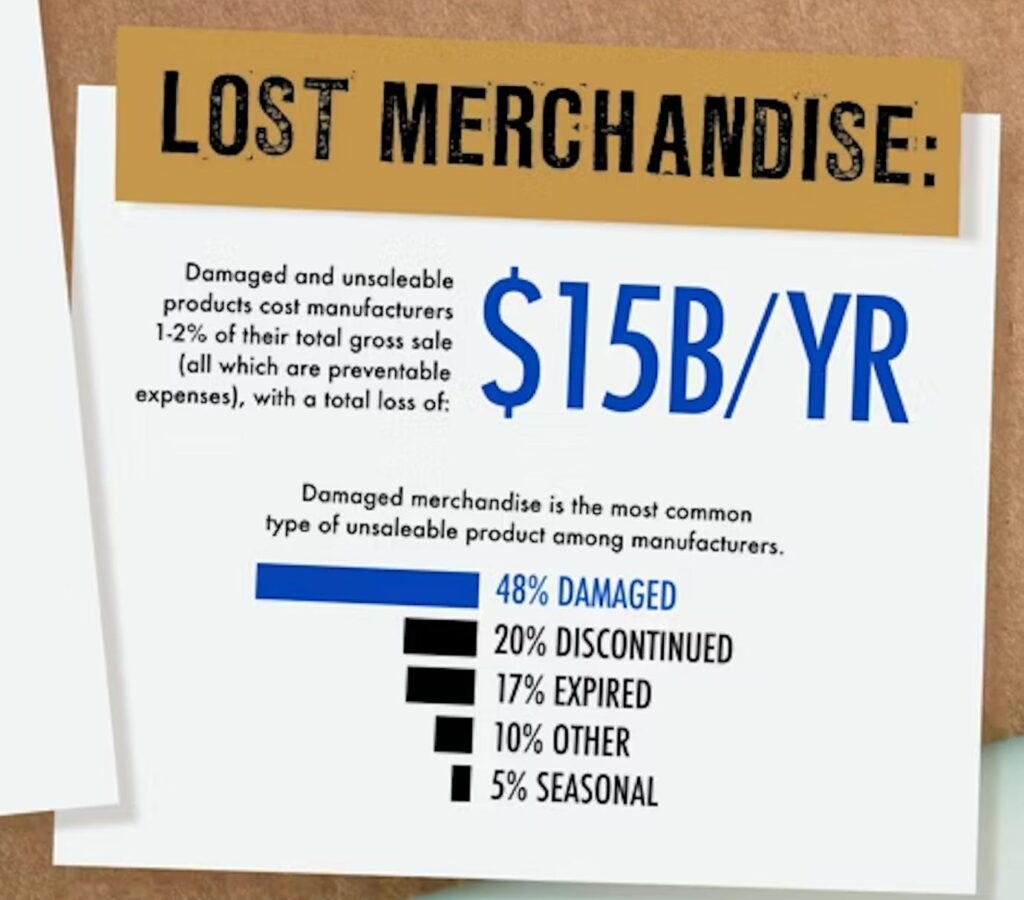