Home » Case Study: Seales Winslow
Case Study: Seales Winslow
The adjustable tension during the cycle is a massive help compared to what we had (pre-fire). There’s no breakage and no time wasting anymore.
- After a massive fire gutted a significant part of the Seales Winslow plant the company rose from the ashes with a clear vision for the future and a renewed commitment to evolve and improve its packaging capability.
Tyler Stuthridge
Operations Manager – Seales Winslow Ashburton
A fire broke out in wooden boxes outside the shed. By the time the fire service arrived over half the 5000-square-metre building was alight. The resulting blaze injured three firefighters and reduced the entire packing line and storage shed to charred ashes.
The company went to Aurora Process Solutions and Universal Packaging with a brief for a coordinated focus across filling, conveying, conditioning, labelling, palletising and wrapping. Universal Packaging worked with Aurora Process to assess the previous set-up and made suggestions for a Spinny unit that could offer greater flexibility for what was required.
Throughput is up and inefficiency is down in Ashburton. For a self-proclaimed ‘OCD Operations Manager’, Tyler is also happy with the neatness of the each wrapped pallet, stating, “I certainly like how the wrap’s ‘tail’ is neatly cut and packed away.”
The Seales Winslow team also appreciates all controls are intuitive and easy to use, which makes a significant difference in the speed of day-to-day operation. The busy Ashburton plant is so pleased with the system they’re now recommending it to others.
“For a self-proclaimed ‘OCD Operations Manager’, Tyler is also happy with the neatness of the each wrapped pallet.”
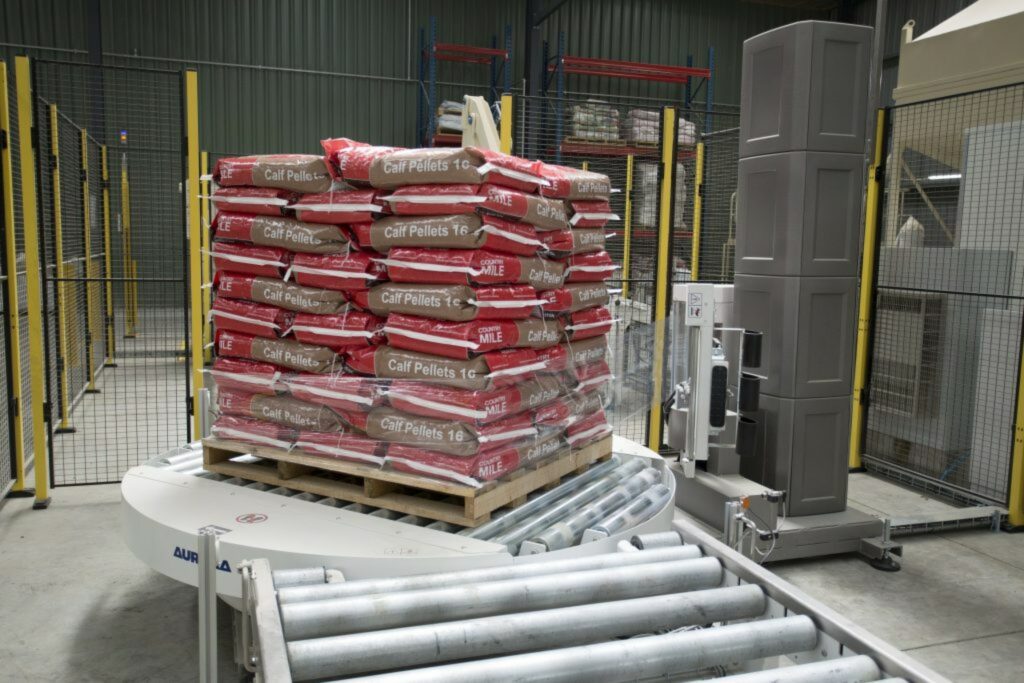
The adjustable tension during the cycle is a massive help compared to what we had (pre-fire). There’s no breakage and no time wasting anymore.
Tagged Spinny