Home » Automation and optimisation
Automation and optimisation
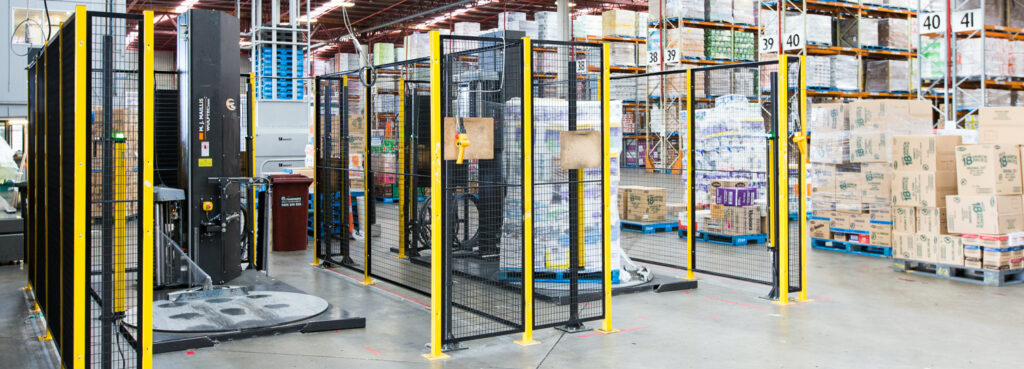
In our experience distribution centres tend to follow relatively predictable changes to growth. However often this growth causes considerable headaches and less than ideal outcomes. Small miscalculations and ‘close enough’ systems can have massive impacts on overall productivity and profitability.
This means optimisation of future throughput needs to be front and centre of all strategic decisions – and it should be considered as early as possible in the growth cycle.
Here are the general phases and the relative considerations for the growing distribution centre.
When hand-wrapping becomes inefficient
For any small-scale distributer, wrapping pallets by hand is a starting point. However, the process is obviously quite labour-intensive so it can inflate distribution costs while also increasing the potential for product damage. The repetitive and physical nature of hand-wrapping pallets is tough on team members and small incidents or absences can create stressful bottlenecks in production and shipping schedules.
At this stage companies looking to improve health and safety conditions for their people (while reducing product damage and labour costs) will generally begin looking around for a semi-automated alternative.
Why semi-automation makes sense
As a company expands so does the throughput. When smaller operators need to increase throughput, they usually move from hand wrapping to a semi-automatic stretch wrapper. This is a logical first step to cope with growth. Semi-automation of the pallet wrapping process not only saves time but also reduces pallet film wastage.
How full automation can often be the only way forward
As the need for faster and more efficient wrapping intensifies, so does the appeal of full automation. Large-scale distribution centres are likely to consider adding a fully automated pallet wrapper, perhaps two, to their pick-stage-dispatch flow. These DCs will often step up to the Wulftec range of rotary-arm wrappers – equipment that allows stationary loads to be wrapped quickly and securely no matter the shape or weight.
Making the most of space and time
Site optimisation for large distribution operations considers the long-term space and time efficiencies offered by various combinations of machinery, process, and layout options.
Redesigning this process is best undertaken by experts. That’s because, when it comes to correctly scoping and entrenching the right system to optimise flow, there are a huge number of details to get right.
Our team has analysed numerous distribution centre designs. After careful analysis and measurement, they know the figures behind every pick-up and put down. More importantly, we understand how small layout issues can turn seconds into minutes into hours of lost productivity. We also know how to prevent these seconds from occurring in the first place.
Sometimes it’s moving the location of a wrapping unit to halve the waiting time for forklift operators. Other times it’s installing safety barriers to protect staff without protracting pack time.
Sometimes our target is to increase sustainability gains by reducing wrap use and by eliminating fuel wastage through unnecessary movement. Sometimes it’s to increase accuracy of pallet protection with new equipment that can pack faster with greater consistency. Quite often it’s all these things (and more).
Whatever your distribution hopes and goals, it pays to have a clear long-term vision in place. To learn more about how we can reduce the steps from pick to dispatch for growing companies around New Zealand, look at our Wulftec machines here.